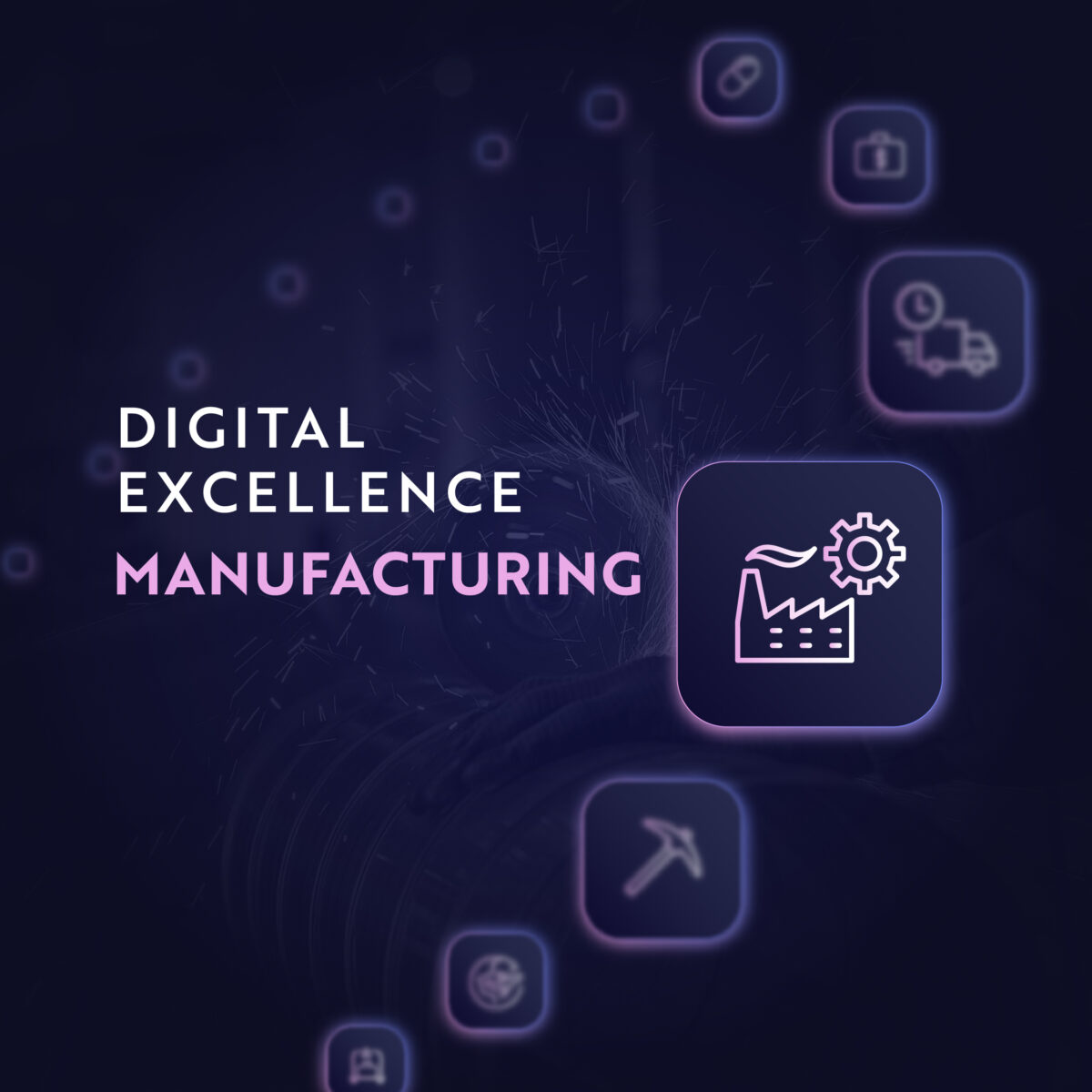
The manufacturing industry is at the forefront of the digital revolution, leveraging advanced technologies to enhance efficiency, drive innovation, and optimize production processes. As manufacturers face increasing pressure to improve quality, reduce costs, and meet evolving customer demands, digital transformation has become a critical enabler of success. This article explores how digital technologies are reshaping the manufacturing industry and provides strategic insights for executives seeking to achieve digital excellence in manufacturing industry.
Key Technologies Transforming Digital Excellence in Manufacturing
- Internet of Things (IoT):
- Smart Manufacturing: IoT devices enable real-time monitoring and data collection from machinery and equipment, optimizing production processes and reducing downtime through predictive maintenance.
- Supply Chain Optimization: IoT sensors provide visibility into inventory levels, shipment tracking, and supply chain dynamics, enhancing efficiency and transparency.
- Artificial Intelligence (AI) and Machine Learning:
- Quality Control: AI-powered vision systems inspect products for defects, improving quality assurance and reducing waste.
- Predictive Maintenance: AI algorithms analyze equipment data to predict maintenance needs, preventing unexpected failures and minimizing downtime.
- Robotics and Automation:
- Industrial Automation: Robots and automated systems perform repetitive tasks with precision, increasing production speed and consistency while reducing labor costs.
- Collaborative Robots (Cobots): Cobots work alongside human operators, enhancing flexibility and efficiency in manufacturing processes.
- Additive Manufacturing (3D Printing):
- Rapid Prototyping: 3D printing enables quick and cost-effective prototyping, reducing development times and facilitating innovation.
- Custom Manufacturing: Additive manufacturing allows for the production of customized parts and products, meeting specific customer requirements and reducing material waste.
- Digital Twins:
- Virtual Simulation: Digital twins create virtual replicas of physical assets, enabling manufacturers to simulate production processes, test scenarios, and optimize performance before implementation.
Benefits and Challenges of Digital Excellence in Manufacturing
- Benefits:
- Increased Operational Efficiency: Digital technologies streamline production processes, reducing costs, improving resource allocation, and increasing productivity.
- Enhanced Product Quality: AI and automation improve quality control and reduce defects, resulting in higher-quality products and customer satisfaction.
- Faster Time-to-Market: Advanced technologies accelerate product development and manufacturing processes, enabling manufacturers to respond quickly to market demands.
- Challenges:
- Technological Integration: Integrating new digital technologies with existing systems requires careful planning and investment, particularly for legacy manufacturers.
- Cybersecurity Risks: The increased reliance on digital technologies exposes manufacturers to cyber threats, necessitating robust security measures.
- Skill Gaps: The adoption of advanced technologies requires a workforce with new skills and expertise, highlighting the need for training and development.
Digital Excellence in Manufacturing: Strong Use Cases
- Predictive Maintenance in Manufacturing:
- Companies like Siemens use AI and IoT to monitor equipment health and predict maintenance needs, reducing downtime and increasing operational efficiency.
- 3D Printing for Custom Manufacturing:
- Aerospace manufacturers like GE Aviation leverage 3D printing to produce complex engine components, reducing weight and material waste while enhancing performance.
- Digital Twins for Process Optimization:
- Automakers like BMW utilize digital twins to simulate production processes, identify inefficiencies, and optimize performance, reducing costs and improving quality.
Compelling Case Studies
General Electric: IoT-Enabled Smart Manufacturing
General Electric (GE) has implemented IoT technology across its manufacturing facilities to enable smart manufacturing. By collecting real-time data from machinery and equipment, GE optimizes production processes, reduces downtime, and enhances efficiency. This approach demonstrates the transformative potential of IoT in manufacturing operations.
Adidas: Robotics and Automation in Production
Adidas has embraced robotics and automation in its Speedfactory facilities to produce athletic footwear. By leveraging automated systems, Adidas increases production speed and flexibility, enabling rapid response to changing consumer demands and reducing time-to-market.
Main Recommendations
- Invest in IoT and AI Technologies:
- Prioritize investment in IoT and AI technologies to enhance real-time monitoring, predictive maintenance, and quality control. Embrace data-driven decision-making to improve efficiency and product quality.
- Enhance Manufacturing Flexibility:
- Leverage robotics, automation, and 3D printing to enhance manufacturing flexibility and responsiveness. Adopt technologies that enable customization and rapid prototyping to meet evolving customer demands.
- Utilize the Digital Maturity Index (DMI):
- Conduct regular DMI assessments to evaluate digital capabilities, identify gaps, and develop strategic roadmaps for transformation. Use these assessments to guide decision-making and prioritize initiatives.
- Strengthen Cybersecurity Measures:
- Implement robust cybersecurity strategies to protect digital assets and sensitive information. Ensure compliance with industry standards and regulations to safeguard against cyber threats.
- Develop a Skilled Workforce:
- Invest in training and development programs to equip employees with the skills needed for advanced manufacturing technologies. Foster a culture of continuous learning and innovation to support digital transformation.
Conclusions
The manufacturing industry is undergoing a digital transformation that presents both challenges and opportunities. By embracing digital technologies and focusing on efficiency and innovation, manufacturers can unlock significant business value and maintain a competitive edge. Executives must prioritize digital transformation initiatives and leverage tools like the Digital Maturity Index to guide their journey toward digital excellence in manufacturing. In doing so, they can drive sustainable growth and profitability while delivering high-quality products in a rapidly evolving market.